FEATURE ARTICLE, JUNE 2006
TRENDS IN BUILDING CONSTRUCTION
Contractors discuss the latest developments in the construction industry. Interviews by Dan Marcec
Northeast Real Estate Business recently interviewed several contractors active in the Northeast commercial real estate market in order to gauge the current climate of the construction industry. Participants include Thomas Tripp, executive vice president of Calamar Construction Management in Wheatfield, New York; H. Wesley Schwandt, director of construction and development for The Buccini/Pollin Group in Wilmington, Delaware; James Thompson, vice president at Pinncon in Braintree, Massachusetts; and David Poloni, president of Iron Hill Construction Management Corporation in Bethlehem, Pennsylvania.
NREB: What trends are you seeing in the construction industry?
Tripp: We are seeing very unusual cost escalation, in materials and related subcontracts. Over the last few years, it has not been unusual to see spontaneous 10 percent increases. This has put a real strain on contracts, profits and relationships with our subcontractors and clients. At the same time, we are seeing a dramatic shortage of skilled labor, both in the trades and in the professional careers, and there is a trend toward more detailed and complex information technology systems, which are intended to save time and effort, though they often provide information overload at all levels of the industry.
Schwandt: Heavy work load, qualified labor shortage, and increased prices.
Thompson: In the retail and commercial arena, timeframes continue to shrink, and the general contractor is expected to assume more responsibility in pulling together all aspects of the project through the construction phase.
Poloni: The industry appears to be moving towards the pre-fabricated society that offers better quality control, more accurate cost accountability, expedited construction duration and reduced labor exposure.
This is all in an attempt to make the business better, quicker and faster. Unfortunately for the Owner, the cost for pre-fabrication is the lack of flexibility and identity. The design/build method of delivery that we employ addresses this.
NREB: How would you describe the costs for materials as of late?
Thompson: Unpredictable. Owners are reluctant to understand that in the time it may take them to make a decision to proceed with a project, construction costs on some items may increase by up to 5 percent. It’s difficult for general contractors and subcontractors to hold their pricing for more than 30 days.
Poloni: Somewhat unpredictable. Prior to 2003, construction material pricing had been stable with a few rare exceptions. Since 2003, we have experienced and/or are currently experiencing major price escalation in the three main components: concrete, steel, and petroleum based products. It seems that the Chinese Industrial Revolution, the War in Iraq and Hurricane Katrina cleanup have taken tolls on our industry.
NREB: What materials in particular have seen price spikes?
Tripp: The most significant sudden increases were in metal products, which were impacted by global demand; however, all product pricing has become quite volatile.
Schwandt: Anything that energy costs can affect.
Poloni: The greatest pricing instability is reflected in petroleum and petroleum-based products. Everything from the fuel used for excavation equipment and material deliveries, PVC/plastic piping, asphalt, petroleum-based insulation products, roofing membranes, and related items have experienced significant price spikes and even shortages over the past 12 to 18 months.
NREB: How do changes in costs for materials affect the industry?
Tripp: Unforeseen cost increases affect contractor profits, but perhaps even more importantly, they affect our client relationships. Our clients, the building owners, are facing cost increases that have not been budgeted, and are surprised and dismayed at very erratic contractor and subcontractor bidding.
Poloni: The entire industry has been affected across the board, from material suppliers, sub-contractors, contractors, and owners; all have absorbed their fair share of the cost escalation. The results are tighter profit margins shared by all and thoughtful consideration of each expenditure by the owners.
NREB: What can contractors do to help developers/owners manage and budget construction costs?
Tripp: Contractors need to manage their risk. We need to get involved with projects earlier, when design decisions are being made, and work with the clients to allocate the risk of the material costs properly. In many cases, owners feel that the contractor should take all the risk, but this is often not in the owner’s best interest.
Specifically, contractors, if involved early enough, can schedule the projects for early procurement, which simply shifts the risk lower down the chain to the suppliers and manufacturers. Alternatively, the contractors can work jointly with the clients to manage the risk together as a team.
Poloni: Contractors should identify areas currently experiencing pricing instability and attempt to tie this volatility into a commodity index to be used as a cost barometer. In addition, contractors should review construction costs regularly and provide updated pricing input. If practical, contractors should research options or alternates for further consideration.
NREB: How does your company strive to keep construction costs down/under control?
Schwandt: With quick pay, involving or creating a trade leader, and better planning.
Thompson: We look at our annual purchasing power on items that we buy routinely, and negotiate rates that remain stable for the year. Unfortunately, these items account for a small percentage of the total project cost. Many suppliers are unable to lock in pricing.
NREB: How is the contractor’s job changing?
Tripp: The industry is changing, involving the construction professionals earlier in the preconstruction, to help the owner and designer make decisions that are more construction friendly. By being involved in preconstruction, we can work to save time and money by proactive preconstruction cost estimating and constructability reviews. In spite of this early involvement, contractors are taking more risk in materials procurement than ever before.
With the advent of the information technology, we are all being inundated with information. Historically, much of the information was being handled by excellent, experienced project management individuals, and provided to others as filtered by them. Now, with the advent of technology, all information is available to everyone in the process, and often the system gets bogged down. I have seen more emphasis on information dissemination than on information quality.
Thompson: The contractor is expected to manage more of the overall aspect of the project, from dealing with the town officials, neighbors, state agencies, many of the authorities that can have an impact on the outcome of a project. Many owners rely on the general contractor to handle anything that comes up.
Poloni: We are placing greater emphasis on design research and pricing feasibility analysis due to current pricing shifts and new governmental regulations. Our experience in project development & site/building designs added to knowledge of construction methods and costs is crucial. We are able to inform our clients fully regarding all options available to them before they make an investment.
NREB: How is technology affecting your job? Your workload?
Tripp: Technology can be a powerful tool to improve productivity; however, in our industry it often has gone beyond improving efficiency. Some of the technology that we have seen in our industry seems to be a solution looking for a problem. The flood of information can become crippling. Many individuals in the construction industry are becoming more information managers than construction project managers.
Thompson: Good news, bad news. While email is a valuable tool, I still prefer to have a 5 minute phone conversation to take care of issues. The back and forth of email is tedious and removes the personal element from the process. The good news is that the instant exchange of documents and drawings is invaluable.
Poloni: Technology is an essential tool in our industry. Through the use of technology, we are able to receive and distribute information to the proper professionals almost instantaneously, modify/adjust designs expeditiously, and construct accurately.
We are constantly honing our processes as new technology becomes available. By utilizing technology and implementing new systems, we have been able to increase efficiency and productivity without increasing the number of employees.
NREB: What are your predictions for changes in the construction industry in the next 5 years?
Tripp: As we go forward, my biggest concern is the continued “brain drain” from the construction industry. My prediction is that it will be even harder to find qualified, interested tradesmen and managers.
NREB: What would you like to see in the construction industry over the next 5 years? Why?
Tripp: We need a concerted effort to attract new talent into our industry, both tradesmen and professionals.
I am also advocating simplified information technology systems, so that the construction project management process can be simplified, making the project managers more involved in the technical solutions and less involved in information management and control.
Thompson: I’d like think that a more cooperative effort between owners and general contractors would result in better, faster, more successful projects for all involved. General contractors have a unique viewpoint to add to the process, and can provide benefit in the areas of costs, schedule and leadtime to help drive projects to success.
Poloni: I would like to see a firm governmental commitment to maintain lower interest rates. As history points out, lower interest rates will feed capital reinvestment continually. In addition, in light of today’s pricing instability, that would help ease the sting of material cost escalation.
Calamar Construction Management
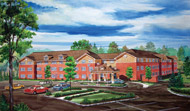 |
Rivercrest Senior Housing in Wheatfield, New York.
|
|
Name: Rivercrest Senior Housing
Location: Williams Road, Wheatfield, New York
Description: Three story wood frame senior housing complex
Property type: Senior Housing
Owner: National Church Residence
Co-Developers: National Church Residence, Calamar
Other Companies working on Project:
Architect: George Lukascevicz
General Contractor: Calamar
Mechanical Contractor: Spark Plumbing & Heating
Plumbing Contractor: David Gross
Electrical Contractor: DeLorenzo Electric
Framing Contractor: David Burke Contracting
Challenges: I. Materials management, including price increases and delivery problems.
II. Insurance issues. The insurance industry is changing constantly and the relationship among the building owners’ insurance requirements, the general contractors’ insurance requirements and the subcontractor’s insurance requirements is creating significant issues in the construction industry, especially in New York. |
The Buccini/Pollin Group
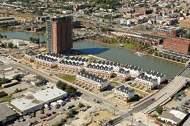 |
The Residences at Christina Landing, an apartment community in Wilmington, Delaware.
|
|
Name of project: Residences at Christina Landing
Location: Wilmington, Delaware
Description: 173 Residential Apartment Units
Property Type: 23 Story Residential Tower
Owner of project: The Buccini/Pollin Group
Other companies working on this project: Gilbane Building Company & Kling Lindquist
Challenges you’ve faced working on this project: There have been environmental challenges. In addition, the project was built next to the Christina River. |
Iron Hill Management Corporation
Name of project: Receivable Management Services (RMS)
Location: 246 Emery Street, Bethlehem, Pennsylvania
Description: 80,000 Sq. Ft. Headquarters and Customer Service Center
Tenants, if applicable: Receivable Management Services (RMS)
Owner of project: J. G. Petrucci Co., Inc.
Developer: J.G. Petrucci Co., Inc.
Other companies working on this project: Iron Hill Construction Management Corporation
Challenges you’ve faced working on this project: It is situated in Lehigh Valley Industrial Park VII, part of the former Bethlehem Steel plant site, and the largest Brownfield redevelopment project in the state. Other challenges are coordination of environmental remediation required with state agencies, and coordination with constructors of Lehigh Valley Industrial Park infrastructure. It is also the first office project in Lehigh Valley Industrial Park VII.
No photo available |
©2006 France Publications, Inc. Duplication
or reproduction of this article not permitted without authorization
from France Publications, Inc. For information on reprints
of this article contact Barbara
Sherer at (630) 554-6054.
|