FEATURE ARTICLE, AUGUST 2011
GREEN RETROFITS: ECO-FRIENDLY AND BOTTOM LINE-SAVVY
Skanska helps clients compare lifecycle costs to understand the benefit of eco-friendly retrofits. By Paul Hewins and Ed Szwarc
While people tend to focus on the carbon that cars emit, the truth is that most of the carbon dioxide in our atmosphere comes from energy consumed by buildings — most likely old ones, with little insulation, outdated mechanical systems and single-glazed windows. New sustainable buildings are increasingly in demand, but energy-efficient retrofits on existing buildings are often more cost effective, less disruptive and ultimately better for the environment.
Old and inefficient buildings, which make up approximately 80 percent of buildings in Northeast cities, can and should be retrofitted to be more energy efficient — not just for environmental reasons but because it makes sound economic sense.
According to the United States Green Building Council (USGBC), buildings that feature high-performance systems can reduce water usage by 40 percent and can cut energy use in half. The resulting reductions in water and energy bills go directly to the owner’s bottom line. The USGBC estimates that businesses that “green” their buildings can anticipate an 8 to 9 percent decrease in operating costs.
Existing buildings already have a “carbon advantage.” The energy required to manufacture their materials and systems and to construct them has already been spent. Even new buildings designed with sustainability in mind fill landfills with the debris of the old buildings they replace. In addition, new buildings consume energy and produce carbon during the fabrication, shipping and construction process.
Retrofits make financial and environmental sense, and people are beginning to notice. In the U.S., retrofits grew from 2 percent of the total construction market in 2008 to an estimated 30 percent in 2010. At Skanska, we have realized the benefits of retrofitting firsthand. Two years ago, we moved into our flagship office at the Empire State Building in New York City, retrofitting our tenant space to achieve LEED Platinum certification, reducing our electricity costs by 57 percent compared to our former office. The Empire State Building fit out is projected to save Skanska roughly half a million dollars in electric costs over the life of a 15-year lease. By changing the cost argument from initial costs to lifecycle value, we were able to do what’s good for the environment and what’s good for our business.
Our clients in Pennsylvania share this experience. Additions to the Swarthmore College Unified Science Center provided new space, linked existing buildings together, and added new sustainable elements. In 2004, the building earned LEED certification. It included a water collection system that collects 100 percent of the water needed to irrigate the entire campus. Almost all of the work spaces have direct access to views of the outdoors and abundant natural light, which saves electricity, reduces operational costs, and has a positive effect on worker morale, likely enhancing productivity.
Pennsylvania remains an important center for pharmaceutical and medical research, with a pressing need to refurbish aging laboratories that use more electricity and water than most other building types. A laboratory Skanska recently renovated was designed with green in mind. The project upgraded water systems to reduce both potable water and process water use. Providing natural light to 84 percent of the space and installing light sensors achieves substantial energy savings.
Renewable energy is part of the solution to carbon reduction.
Building owners aren’t limited to building new buildings to realize the benefits of high-performing green/LEED buildings. Most major building systems have a useful life of 25 to 35 years. When systems are about to fail, they need to be replaced anyway. This is the time to invest a little more in thoughtful, cost-effective retrofits, bringing buildings into the 21st century for a relatively small incremental cost.
Even changes to a building’s exterior can result in major energy savings. Skanska is currently working on installing a 1,500-kilowatt fixed solar photovoltaic system for the Merck Sharp & Dohme Corporation in Upper Gwynedd, Pennsylvania. The project will reduce Merck’s on-site carbon footprint by 12 percent by 2012 and improve energy efficiency by 40 percent. The project also includes the installation of an electric car recharging station, which will create the first known zero-emission car fueling station in the state.
Last summer, Skanska Koch, part of our Skanska USA Civil division, installed a solar power generation system to reduce its energy consumption and lower the environmental impact of its Carteret, N.J., headquarters. Consisting of 1,617 solar panels — each fixed to the roof of the Skanska Koch facility — the system will provide approximately 85 percent of the electrical needs of the facility. The new solar panel system is also expected to reduce annual carbon dioxide emissions by the equivalent of burning more than 38,000 gallons of gasoline.
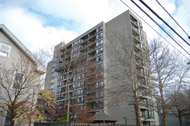 |
Skanska is working with the Cambridge Housing Authority to implement green retrofits at the Lyndon B. Johnson Apartment complex. The updated project will feature the largest solar panel installation in Cambridge, Massachusetts.
|
|
In Massachusetts, we are working closely with the Cambridge Housing Authority (CHA) to make the Lyndon B. Johnson Apartment complex one of the greenest buildings in the city. The apartment complex, a public housing development for senior and disabled residents, was first occupied in October of 1973. The five- and 12-story high-rise building was made of cast concrete with an electric heating system, which was efficient and cost-effective when built. But the building has gone through few substantial renovations, and is in desperate need of repair. With the help of $10 million from the American Recovery and Reinvestment Act, CHA is committed to a “transformative change” in the approach to energy use at the property, with the largest solar panel installation in Cambridge. The Skanska project team will also install a co-generation system to augment the onsite gas and electricity systems. The old, outdated energy systems will be replaced by highly efficient gas-fired heating and a central cooling system. New high performance window-walls and a complete re-cladding of the building will add an extra layer of insulation.
When considering retrofits, we urge our clients to consider the lifecycle costs of a project. All told, the LBJ Apartments, which is scheduled for completion next year, will consume 50 percent less energy than it did before the renovations, saving roughly $255,000 in energy costs per year. This will reduce CHA’s carbon footprint by 2.5 million pounds a year.
Small, inexpensive retrofits and upgrades can help bring buildings with 20th century bones into the new millennium. They will also help the environment — and business owners’ wallets.
Paul Hewins is general manager and executive vice president for Skanska USA’s New England region. Ed Szwarc is general manager and executive vice president for Skanska USA’s Greater Philadelphia region.
©2011 France Publications, Inc. Duplication
or reproduction of this article not permitted without authorization
from France Publications, Inc. For information on reprints
of this article contact Barbara
Sherer at (630) 554-6054.
|